Fraunhofer-Gesellschaft macht Solarzellen besser, schneller, billiger
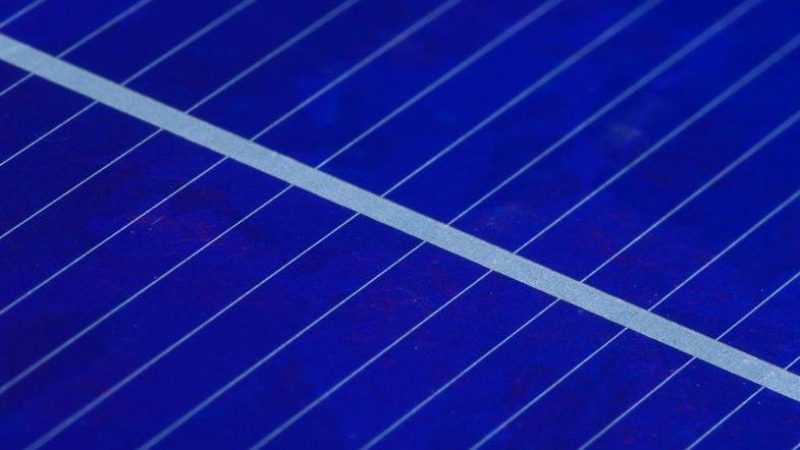
In Hamburg dreht sich vom 5. bis 9. September 2011 alles um unseren größten Energielieferanten, die Sonne. Fraunhofer-Forscher stellen auf der EU PVSEC, der European Photovoltaic Solar Energy Conference, in Halle B4G, Stand C12, neue Methoden vor, mit denen man Solarzellen billiger und effizienter machen kann.
Auf vielen Hausdächern, besonders in Süddeutschland, glänzen inzwischen die schwarzen Platten der Solarzellen. Oft sind es Solarkollektoren, die für Heißwasser sorgen, immer öfter auch Photovoltaik-Anlagen, die das Sonnenlicht direkt in Strom umwandeln. Aber bisher kommen nur etwa zwei Prozent des Stroms in Deutschland aus Solarenergie, denn noch sind Solarzellen vor allem in der Produktion teuer und aufwändig.
Wissenschaftler der Fraunhofer-Gesellschaft entwickeln innovative Herstellungsverfahren, um das zu ändern. Vor allem Laser eröffnen in der Fertigung von Solarzellen ganz neue Möglichkeiten. „Die Lasertechnik ermöglicht kontaktloses, präzises und schnelles Bearbeiten“, erklärt Dr. Malte Schulz-Ruhtenberg vom Fraunhofer-Institut für Lasertechnik ILT in Aachen den Hauptvorteil. So lassen sich bessere Solarzellen kostengünstiger produzieren.
Laserverfahren hoch im Kurs
Ein Beispiel ist das Hochrate-Laser-Bohren, welches sehr präzise und schnell kleine Löcher in Solarzellen erzeugt. Wozu man das braucht? Eine klassische Solarzelle erzeugt Strom durch den photoelektrischen Effekt. Sie besteht aus mehreren leitenden und halbleitenden Schichten. Fällt Licht auf die Solarzelle, werden negative Ladungsträger aus ihrer Bindung gelöst und es fließt elektrischer Strom.
Bisher befinden sich auf Vorder- und Rückseite der Solarzellen die Kontakte, um den so erzeugten Strom abzutransportieren. Wenn alle Kontakte an der Rückseite verlegt werden können, wo sie keine Schatten werfen, steigt der Energiegewinn. Die Löcher in den Solarzellen schaffen die Voraussetzungen für diesen Ansatz, der als „Emitter-Wrap-Through“, kurz EWT, bezeichnet wird. Um noch höhere Geschwindigkeiten und damit höheren Durchsatz zu erzielen, können spezielle Polygon-Scanner eingesetzt werden.
Bei diesen Laser-Scannern lenken rotierende Polygon-Spiegel extrem schnell aufeinanderfolgende Laserpulse gezielt ab und sind so in der Lage sehr schnell große Flächen zu bearbeiten. „Das ist eine vielversprechende Technologie, die für viele Laserprozesse eingesetzt werden kann“, so Schulz-Ruhtenberg.
Genau und schonend fürs Material
Neben der Geschwindigkeit spielt auch die schonende Arbeitsweise der Laser eine große Rolle in der Solartechnik, denn die Zellen und Wafer, also die Grundelemente der Solarzellen, sind empfindlich. Laserstrahlen sind aber so fein dosier- und kontrollierbar, dass die Zellen kaum belastet werden.
Deshalb nutzten die Fraunhofer-Forscher sie für fast alles: um zu bohren, zu schmelzen, zu schneiden oder auch zu löten. Zum Beispiel werden Ultrakurzpuls-Laser eingesetzt um Vorder- und Rückseite der Solarzellen voneinander zu isolieren.
Sie arbeiten schonender als andere Methoden und das ist wichtig, denn ein großer Anteil der Kosten von Solarzellen geht auf Schäden und Bruch in der Produktion zurück.
Roboter im Test
Schäden verursachen häufig auch die Handhabungsroboter, die in unterschiedlichen Varianten von allen Herstellern eingesetzt werden. Sie sollen möglichst schnell und genau arbeiten, aber ohne die empfindlichen Teile zu beschädigen − das senkt die Kosten.
Am Fraunhofer-Institut für Produktionstechnik und Automatisierung IPA in Stuttgart arbeiten Forscher daran, die automatisierte Handhabung von Wafern und Solarzellen zu verbessern. „In unserem Test- und Demonstrationszentrum versuchen wir, die Handhabung und Automatisierung in der Photovoltaik nachzustellen und so zu optimieren“, erklärt Roland Wertz, der Verantwortliche beim IPA.
Es dient dabei als Schnittstelle zwischen industrieller Fertigung und Forschungsdienstleistung im Bereich Automatisierungslösungen. So werden unter möglichst realen Bedingungen alle Einflüsse und Parameter registriert, die sich zum Beispiel auf die Genauigkeit und Geschwindigkeit verschiedener Greifsysteme auswirken.
Dabei hilft der Roboter ABB IRP 360, auch FlexPicker genannt, der auch am Fraunhofer-Stand ausgestellt wird. Er wird als Manipulator zusammen mit dem eigentlichen Greifer für Experimente genutzt. So analysieren und bewerten die Wissenschaftler Produkte unterschiedlicher Hersteller und mit verschiedenen Wirkprinzipien. Denn jede konkrete Anwendung hat eigene Anforderungen und verlangt damit nach eigener optimierter Handhabung.
Weniger ist mehr
Aber nicht nur in der Produktion wird gespart und optimiert, sondern auch beim Material. Nicht mehr als unbedingt nötig − das ist das Prinzip von Dünnschicht-Solarzellen. Sie bestehen meist aus einem preiswerten Träger, auf den das elektrisch aktive Material als ultradünne Schicht aufgebracht wird. Um Dünnschicht-Solarzellen qualitativ hochwertig und dabei kostengünstig herstellen zu können, hat das Fraunhofer-Institut für Schicht- und Oberflächentechnik IST in Braunschweig verschiedene Verfahren für jeden einzelnen Produktionsschritt entwickelt.
Die Halbleiterschichten, das Herz der Zelle, werden zum Beispiel mit dem Hot-Wire-CVD-Verfahren hergestellt. „Der Vorteil gegenüber herkömmlichen Verfahren ist die schonende Form der Schichtherstellung“, erklärt Dr. Volker Sittinger vom IST.
Bei herkömmlichen plasmaaktivierten CVD-Verfahren ist das Material während der Beschichtung dem Beschuss mit hochenergetischen Teilchen ausgesetzt. Anders bei der Hot-Wire-CVD: Dort werden die schichtbildenden Gase nicht in Plasma, sondern an heißen Drähten angeregt. So entstehen auf schonende Weise hochwertige Schichten.
Außerdem lässt sich das für die Herstellung nötige Silangas besser nutzen. „Wir wandeln bei der Hot-Wire-CVD bis zu 90 Prozent der eingesetzten Gase in Schichtmaterial um und erreichen dadurch auch höhere Beschichtungsraten als bei herkömmlichen Prozessen“, sagt Sittinger.
Für die Kontaktschichten auf Front- und Rückseite gibt es seit Kurzem die C²-Beschichtungstechnologie (Cylindrical Magnetron Co-Sputtering). Sie ermöglicht es, die Materialzusammensetzung während der Beschichtung der Solarzelle zu variieren.
Und es soll noch dünner gehen. Mit einem neuen Typ dreidimensional aufgebauter Solarzellen könnten wenige Nanometer dünne Schichten möglich sein. Das geht nur mit konturgenauer Abscheidung der Schichten, aber auch dafür gibt es eine Methode: ALD, das steht für Atomlagenabscheidung, aus dem Bereich der Nanotechnologie.
Solarzellen müssen also nicht mehr so teuer sein. Denn neue Technologien könnten die Solarenergie einen großen Schritt nach vorne bringen. (rls / idw)
vielen Dank, dass Sie unseren Kommentar-Bereich nutzen.
Bitte verzichten Sie auf Unterstellungen, Schimpfworte, aggressive Formulierungen und Werbe-Links. Solche Kommentare werden wir nicht veröffentlichen. Dies umfasst ebenso abschweifende Kommentare, die keinen konkreten Bezug zum jeweiligen Artikel haben. Viele Kommentare waren bisher schon anregend und auf die Themen bezogen. Wir bitten Sie um eine Qualität, die den Artikeln entspricht, so haben wir alle etwas davon.
Da wir die Verantwortung für jeden veröffentlichten Kommentar tragen, geben wir Kommentare erst nach einer Prüfung frei. Je nach Aufkommen kann es deswegen zu zeitlichen Verzögerungen kommen.
Ihre Epoch Times - Redaktion